Long read
Taking the chill off cold storage: Challenges and solutions for the cold chain
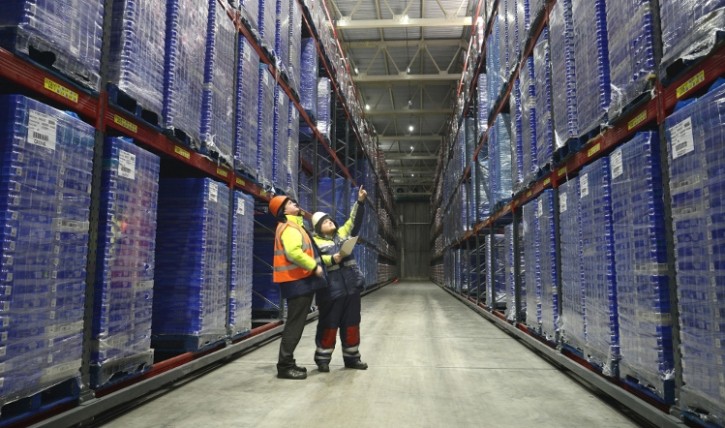
The word ‘resilience’ has become synonymous with the UK’s cold chain over the past five years. The temperature-controlled storage and distribution industry has navigated crisis after crisis during this time, to continue performing its vital role as the lynchpin of the food supply chain. The lasting impact is clear: our recent survey results show that 74% of UK cold chain operators consider that the industry has emerged from these challenges even more resilient than it was before.
Despite this backdrop of great challenge and disruption, in the UK the past five years have continued to be a time of significant growth for cold storage. There has been very strong demand for cold storage space and the industry has continued to grow with significant investment both from abroad and from within the UK.
Last year the volume of cold storage space operated by Cold Chain Federation members passed the milestone of 40 million cubic metres and there are several large cold stores currently being built by third party logistics operators.
Our industry has also made notable strides forward in certain key areas during this challenging time. A number of advances which were already underway have been accelerated significantly as a result of the adversities operators have needed to navigate. Improving energy efficiency in cold storage is a prime example.
Cold stores had been making improvements in energy efficiency over the past decade, prompted by regulations, customer requirements and tax savings under the Climate Change Agreement for cold stores. However, the drive to reduce energy consumption intensified as energy prices skyrocketed during 2022.
Investment in energy efficiency
Increased investment has been made industry-wide in the energy efficiency of buildings, equipment and processes over the past two years and is not only helping operators to reduce the rises in their energy bills, but are also helping to protect operators against future volatility in the energy market.
There has been a growing focus on increasingly sophisticated measurement and analysis of energy usage. Sub-metering and scrutiny of live data are enabling leading-edge operators to identify precisely where and when a cold store’s energy use could be made more efficient, where current wastage could be avoided, and where refrigeration system operation could be improved.
Many cold stores in the UK have invested in improving the insulation of the building envelope, in approaches that minimise ingress through doors and openings, in efficient use of LED lighting, and in automation. Improvements to the operation and maintenance of key cold store equipment such as refrigeration systems is also playing an increasingly important role in energy efficiency, at a time when seemingly small adjustments in performance can change energy bills by thousands.
Perhaps the most visible impact of the past two years’ accelerated focus on improving the energy efficiency of cold stores has been the huge interest in on-site renewable energy generation. Demand for solar panels in particular has been very strong from cold storage facilities, enabling operators to maintain more control over energy costs in the short and medium terms while also contributing towards longer-term sustainability objectives. CCF data suggests that perhaps as much as 25% of cold stores in the climate change agreement scheme now have solar panels, a figure much higher than in ambient warehousing.
Another example of important changes that have been made in response to a major industry-wide challenge is the progress we are seeing across the logistics industry in recruitment, retention and upskilling of employees.
Cold chain recruitment crisis
Media coverage of the recruitment crisis in logistics as we came out of Covid restrictions focused mostly on drivers, but the shortage of people was felt acutely in warehouse roles and office roles too. These staffing shortages highlighted that the logistics industry as a whole needed to look at modernising its approach to recruiting and retaining the talent it needed, not just to fill vacant roles at that time but also for the future.
Cold chain operators have responded well. Over the past two years the Cold Chain Federation and our members have been working together with organisations across logistics to address challenges around bringing new people into our industry and upskilling for the cold chain of the future.
Supporting the people and cementing the skills that will be needed in the years ahead is central to the ‘Generation Logistics’ campaign to find the next generation of logistics talent, a campaign which the Cold Chain Federation is pleased to support.
For a long time, many job-seekers have been unaware of the breadth of jobs available and the career prospects in the cold chain. In reality, joining the UK cold chain should be seen as a highly desirable career choice, full of opportunity and fulfilment across a variety of roles including warehouse operatives, driving, engineering, sustainability, finance, marketing, HR, digital technology, international trade and increasingly robotics and digital solutions.
Our industry is now promoting far more proactively how and why it can offer great opportunities for people who want to embrace ceaseless innovation, a fulfilling and meaningful career, international travel and leading-edge technology as part of the day job.
This has come alongside investment into supporting and encouraging the next generation of talent as well as improving pay, conditions and career development opportunities for those already working within the industry.
Investment in developing skills
Operators are also investing in developing the skills that will be needed within the industry’s workforce as the cold chain evolves over the decades to come. People in our industry are adapting and learning new skills as the cold chain responds to changing customer requirements, international trade dynamics, technological innovation and the journey towards net zero.
People working throughout the cold chain have certainly shown their mettle in recent years, and operators are rightly proud of their teams. As our industry looks to the future, our people are at the heart of how the cold chain will grow and evolve to meet the nation’s changing needs. We have set out together in the right direction and as demand continues to increase for sustainable and efficient temperature-controlled logistics, it is crucial that we continue to develop our talented people and our skills for the future.
While the energy and recruitment challenges have affected cold stores and their food supply chain partners across the UK, business working in the food chain in Northern Ireland have had to navigate additional challenges unique to the region. Under the Northern Ireland Protocol, cold chain operators working between Great Britain and Northern Ireland have had to contend with great uncertainty, frequent disruption, and hugely increased bureaucratic burden and expense.
While the uneasy status quo just about worked in keeping goods on the shelf, the ‘fudge’ on moving goods from the GB mainland to Northern Ireland was never sustainable. The half-implemented protocol, applied through unilaterally imposed easements, discriminated against small businesses and caused uncertainty and disruption as well as a huge cost burden for businesses, consumers, and taxpayers.
This problem needed a carefully calibrated solution and the announcement of a Green Lane as a key feature of the Windsor Framework initially provided some hope of a much more efficient and sustainable system. However, these hopes have been partially dashed with the publication of the detailed guidance.
Many businesses will look at the conditions and inflexibilities of the green lane and decide the full customs red lane may be the better option, despite the costs. In particular, the ‘not for EU’ labelling requirement is set to mean a major restructuring of supply chain flows. The promise of the green lane approach has not been matched by the reality of the regulations, and it is the professionals in the food supply chain who will yet again have to find a way through.
Import and export to the EU
However, even as the uncertainty and disruption continue for businesses involved in the movement of food from GB mainland into Northern Ireland, the region continues to be one of the most exciting places for cold chain development in the UK.
Businesses are tapping into new opportunities, with innovation and investment that will strengthen the cold chain in Northern Ireland over the coming years and well beyond. Cold storage capacity is growing apace, and the investment in energy efficiency facilities, equipment and training is impressive.
Of course, it’s not in Northern Ireland alone where changes to trade rules are affecting cold chain businesses, those trading with the EU have also had to contend with new and costly processes which have so far hit UK food exporters but are set to have a bigger impact on importers from October.
There is no question that the past five years have presented multiple, major challenges for cold stores across the UK. Many of these challenges including post-Brexit changes, recruitment challenges and inflationary challenges are still playing out with their full impacts remaining to be seen. UK cold storage operators continue to respond with resilience, creativity and determination, and the Cold Chain Federation is supporting them every step of the way.