Slippery when wet
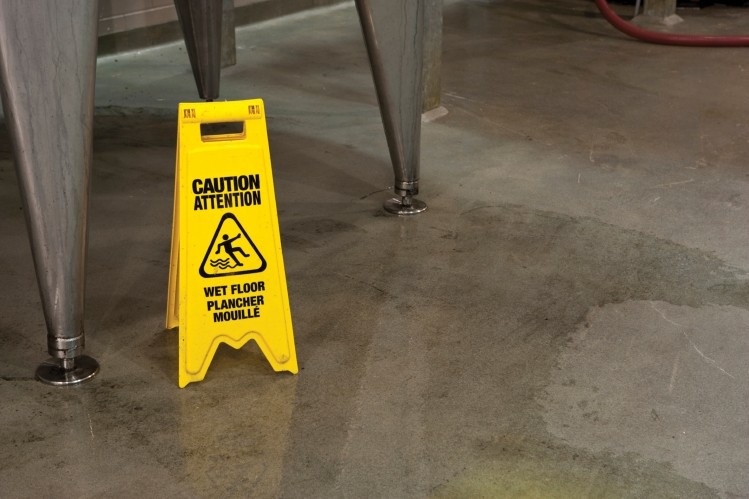
If you're a parent, you'll know there's a big difference between thinking 'accidents will happen' and taking them for granted. The same is true in food and drink processing.
Accidents will happen all right in the year to March 31, the industry reported 4 fatalities and more than 5,200 major injuries and absences to the Health and Safety Executive (HSE). What's more, the number of incidents has fallen annually since April 2000. There's been a drop of 3.5% in the year to March 31 this year and an impressive 52% since 1990.
However, manufacturers and supporting health and safety agencies and trade bodies believe even one incident is one too many. Especially in the light of the harsh penalties awaiting firms falling foul of the UK Corporate Manslaughter and Corporate Homicide Act enforced on April 6 last year.
Fortunately there are high quality campaigns, training packages and tools to tackle the issues. There's also consensus on the areas of greatest concern. Musculoskeletal injuries remain the biggest cause of injury and the treatment of migrant workers needs addressing, as do vehicle-related accidents. Kit maintenance is a big issue and dairy processors top the list of problem sectors.
HSE data indicates the dairy sector reports the highest number of incidents, although there's disagreement on exact figures. Milk roll cages are the biggest concern. More than a third of incidents in the sector are caused by manual handling of these metal trolleys. "When they are filled with milk they can weigh a quarter of a tonne," says Richard Morgan, head of the HSE's food and drink manufacture section. As a result of the hazards they represent, trade body Dairy UK has just published guidance on handling them.
Moving machinery
Moving machinery is another source of problems the fourth highest cause of major workplace injuries and absences for food and drink manufacturers from 2009-2010. But more seriously, it was also responsible for three out of four fatalities in the past year, seven out of 10 since April 2007 and more than a third since April 2000.
"The particular problem here is people accessing machines that haven't been isolated," says Morgan. Often, victims are cleaning or repairing equipment and either someone else unaware of this restarts it or the maintenance itself triggers it to leap into life, he says. In most cases, it's a simple matter of maintenance personnel locking the kit down using a key and retaining it while they work.
Another concern highlighted by insurance broker Jardine Lloyd Thompson (JLT) is vehicle-related incidents. "Some of the big players in the industry renowned for health and safety are concerned that this is not particularly well covered," says Ian Edwards, UK food and drink executive at JLT.
The topic covers everything from fork-lift use in storage areas to distribution and deliveries, he says. "The connection has been made that vehicles are an extension of the workplace and clearly how and where they are used and maintained ought to have similar standards of risk assessment."
Solutions must be tailored to individual sites, as they all have different issues, says Edwards. However, a common problem is irregular housekeeping, with objects such as pallets blocking designated walkways causing staff and visitors to skirt tramlines.
Morgan says incidents occur involving people guiding reversing lorries. "The rule there is they must always be in sight of the driver. They are not there primarily to help the driver reverse, but to keep pedestrians out of the way." Other hazards he mentions are people emerging from offices and crossing yards without high visibility jackets and third-party contractors ignorant of procedure visiting sites out of hours and using the manufacturer's forklifts to unload lorries.
A lot of procedural deviation also occurs when changes take place to workplace structure and environment. For this reason, excellent change management is essential in preventing incidents, says Morgan.
Communication is key
Of course, the best and most flexible procedures in the world won't help if your firm doesn't communicate equally to all sections of the workforce. An Equality and Human Rights Commission inquiry uncovered mistreatment of agency staff, particularly migrant workers, in the meat and poultry industry last month.
As a result, the HSE launched a series of inspections of meat and poultry processors at the beginning of this month. "One in six agency workers interviewed highlighted health and safety issues where they were treated worse than full-time employees," says Morgan. Issues raised included poor provision of personal protective equipment, health and safety assessments for pregnant workers and training; inability to understand training; ignorance of health and safety complaint procedures and Working Time Directive breaches.
Over all these issues the biggest cause of injury across the board remains poor manual handling and resultant musculoskeletal complaints. From 2008-2009 it was responsible for virtually a third of reported injuries or absences, according to the HSE.
Solutions to the problem don't have to be complicated. Pork processor Tulip found that blunt knives made butchers work harder when cutting carcasses, causing stress-related wrist injuries, so it employs knife sharpeners to make sure blades are constantly kept keen, alleviating unnecessary force.
Other answers are more involved. The HSE, with Greencore, has been instrumental in trialling tools such as Back-Track, from the company of the same name. The electronic device is strapped to workers' backs and records movements made while lifting objects. It is now being rolled out across all the company's factories.
"If Back-Track's costs were doubled, I wouldn't call it expensive," says Tom Chambers, Greencore group health and safety manager and vice-chairman of Institute of Occupational Safety and Health (IOSH) management committee. "You can rent the equipment as well." Hot on the heels of Back-Track comes the HSE's Assessment of Repetitive Tasks online assessment tool (ART), targeting upper limb movements.
Proper training
There's also a wealth of training aimed at health and safety issues. The HSE offers many courses supporting its Slips, Trips and Falls campaign now in its third year and its 'Do Your Bit' campaign, exhorting firms to engage employees in solutions. 'Do Your Bit' began last month and will run for a year.
HSE's Slips and Trips eLearning Package (STEP) gives access to introductory, intermediate and advanced level health and safety courses. STEP includes guidance, case studies, videos, animations and quizzes. And the HSE's Work at height Access equipment Information Toolkit (WAIT), advises firms on equipment for work at height.
Aviva Risk Management Solutions (ARMS) provides a host of courses aimed at the industry. Helen Toll, health and safety consultant at ARMS says courses for line managers and supervisors are often neglected and recommends IOSH's Managing Safely course. "A higher level of awareness can be achieved by completing the NEBOSH [National Examination Board in Occupational Safety and Health] General Certificate in Health and Safety," says Toll. She also commends the one day IOSH Safety for Senior Executives course, which can be tailored to the industry, for senior managers.
Yes, accidents will happen, but fortunately there's enough tools to identify and tackle the issues. Of course, that means there's less excuse when incidents do occur.