No weak links in the chain
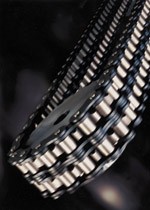
The way goods are moved around the factory impacts on both process speeds and costs and so new technologies making conveyors more reliable and efficient deserve serious consideration. As the most competitive manufacturers have already re-engineered factory floor space to eliminate weaknesses in their production chain, companies that haven't investigated the latest conveyor designs are losing out.
As one company put it, your production line is only as good as its weakest link. But inevitably, it takes active planning to spot and eliminate such weaknesses -- rather than reactive buying when a crisis occurs.
"Manufacturers are looking at changes more strategically, rather than in a reactionary fashion," says Steve Dennett, sales and marketing manager at turnkey projects company Wrightfield. "Companies are looking at where they want to be in two or three year's time. They're being driven by the demands of the supermarkets and realise they've got to get ahead of the game."
This means looking at the most efficient product flow. Wrightfield recently completed a key project for Faccenda, which supplies supermarket chains and restaurants with whole chickens and portions from six sites in the UK. The project involved moving existing lines and installing new equipment in a new building at Brackley.
The project took eight months, with much of that time spent planning and liaising with Faccenda's engineers on the layout of the proposed factory. Once plans were agreed, the installation was carried out over seven weekends to avoid production downtime.
Key aims were to increase throughput, reduce manual activity, improve health and safety, improve hygiene, reduce running costs and retain flexibility.
"The basic principle in increasing productivity is to find the weak links and improve them. There are always processes that slow the rest of the line down or bottlenecks. It is also about reducing manual labour. We try and automate, wherever possible," says Dennett.
The consumer trend towards value-added convenience foods means manufacturers face shorter runs and so want more flexible production space. Compact tier conveyors were utilised by Faccenda to save space and similar concepts are frequently used elsewhere.
"We are doing more of three or four-tier conveyors, one above the other so that the person on the line may pick from one and place defective products on another," says Dennett.
Wrightfield used modular plastic belts supplied by Intralox which have open-hinged belts; fold-down sides and pre-laser-cut cleaning slots to allow better access for cleaning and improved hygiene.
Speed and feed integration, coupled with emergency stop procedures to metal detectors, labellers, bag packers and automated cut-up machines was accomplished using the latest CE-approved electrical and software engineering. Manual lifting was also practically eliminated. "It's not just about making conveyors anymore. Projects involve meeting after meeting to design layouts -- everything is so much more bespoke," says Dennett.
Wrightfield also looks to use motors with the lowest emissions and electricity usage. "In this project we installed drum motors in place of the more traditional drive motors with a gear box, as they are smaller and can be located in the conveyor frame, off the ground. The first generation of drum motors ran rather hot but current designs are cooled and are much more reliable," says Dennett.
Eddie Collins, a spokesman for BDL drum motors and various conveyors, agrees that many of the early problems with drum motors have been ironed out. "Early models were completely sealed and prone to overheating as the cladding acted as an insulator and the oil started to heat and burn. They have changed the oil to one that does not overheat and there are now 170 different profiles for the cladding," he says.
A particular advantage of the drum motor is improved hygiene. "Cogs and rollers are prone to trapping dirt and oil which can contaminate products, whereas motorised drums remove the dirt traps," he adds. The drum motor's neat profile also makes for easy cleaning.
Roller chains are still the conveying choice for heavy-duty process environments involving very high or low temperatures. Chain manufacturers have also worked hard to enhance chain reliability and hygiene. Renold, for example, has improved the fatigue and wear resistance of its chains by reducing the stress on the bearings areas. This dramatically improves chain life. The chain links also have improved stress distribution and beneficial compressive stresses built-in during manufacture to improve their durability.
Tsubaki has also increased the life of its lubrication-free Lambda roller chain and made it easier to disassemble. Oil-impregnated fittings provide internal lubrication between pin and roller. The metal structure and surface hardness of the link plates, rollers and pins has been improved and Tsubaki has used new coating technology and materials to improve corrosion resistance. The chain has an operating temperature range from -10° C to 150° C.
Where dried and dusty ingredients are involved vacuum technology is usually the preferred transfer method. Here Swedish company PIAB has developed the IC33 series of vacuum conveyors based on new patented pump technology that ensures a lower energy consumption than any other compressed air driven conveyor.
Thinner steel belts
A breakthrough in steel belt processing technology has enabled Sandvik to launch super-thin stainless steel conveyor belts. Steel's high thermal conductivity makes it ideal for hot or cold production processes, such as drying, freezing or cooling and enables operation down to -50°C.
Sandvik's new 1700SA stainless steel belt grade is so thin it is a viable alternative to some plastic belts. Available in thicknesses from 0.2mm to 0.6mm and widths from 10mm up to 100mm, the new belts have a low deflection diameter enabling equipment manufacturers to design extremely compact systems with small conveyor drums.
Steel belt systems are seeing growth in the freezing of instant coffee. Coffee is fed on to the steel belt in the form of a uniform, foamy paste. It is then frozen by blasting with cold air at high velocity. The hard smooth, corrosion resistant surface allows easy and clean discharge of the frozen coffee.
With manufacturers producing more product variants and pack sizes, production space is a big issue. Many factories now make use of mezzanine levels, making vertical transfer of materials a frequent requirement.
Conveyor Belt Technology (CBT) supplies space-saving spiral conveyors that enable continuous, smooth vertical transfer of products between levels without the problems associated with inclined belts or lifts. Ideal for emptying high level spiral freezers they can also provide a buffering solution between processing and packaging equipment. Those offered by CBT can bridge heights up to 5m, with belt speeds of up to 30m/min.
Spiral conveyors were installed by Astec to help Walkers Snack Foods increase handling capacity on its packing lines. Filled, taped cartons were being transferred from end of line to robot palletising pick-off positions via high level conveyors and a series of inclined belt conveyors and combine on a common transit conveyor. As space was limited, Astec installed a spiral conveyor here merging it with a common roller conveyor.
Curves are useful for directional changes within tight spaces, but to be reliable they need very good belt tracking. Interroll says its new belt Curve+ has a positive head-drive to ensure reliable transport at up to 1.5m/sec.
The belt is kept on track by spring-loaded castors fitted inside the upper section of the outer radius side frame, and low set castors inside the lower section. These absorb the lateral forces on the belt generated through the curve. The no-slippage positive drive relies on drive teeth under the belt that interlock with the drive sprocket.
It allows a small conveyor height of 180mm, compared with 260mm previously, as well as providing low belt tension, longer service life and easy maintenance.
Line efficiencies are being increased by use of lane dividers and convergers. For Walkers, Astec installed a lane divider prior to the robot cells where a barcode scanner determines whether the carton proceeds to the robot palletising cell. Those with coding errors or misreads are automatically diverted to a manual stack-down station.
To ensure cartons don't pile into each other in the event of a problem, Astec installed zero-pressure accumulating conveyor sections prior to each cell; these restart automatically when the zone in front becomes clear.
Astec was also charged with reducing stoppages due to cartons that had not been taped properly. It installed five compact cameras below the conveyor bed which communicate with PC-based control systems to pre-divert untaped cartons away from palletiser cells.
Today conveyors have to integrate with all kinds of kit, such as sealers, metal detectors and -- looking ahead -- radio frequency identification equipment. As a result, the control side of conveying is getting much more complex and more kit is driven by programmable software. But there is good news, according to Dennett: "Previously software was deemed a bit of a black hole in terms of cost, but it has become more affordable." FM
Key contacts
- Astec Conveyors 01283 210333
- Wrightfield 01379 872 800
- BDL 01336 408899
- Conveyor Belt Technology 01274 689 222
- Interroll 01536 748 565
- Intralox 00 31 20 430 3600
- PIAB 00 46 8630 2575
- Renold 0161 498 4531
- Sandvik 00 49 711 5105 148
- Tsubaki UK 016233 688788